“未来工場”目指すカイゼンで構内物流を自動化。
三菱ふそうトラック・バス株式会社 様
https://www.mitsubishi-fuso.com/ja/
業種:自動車・輸送機器
導入商品:AGV・AMR
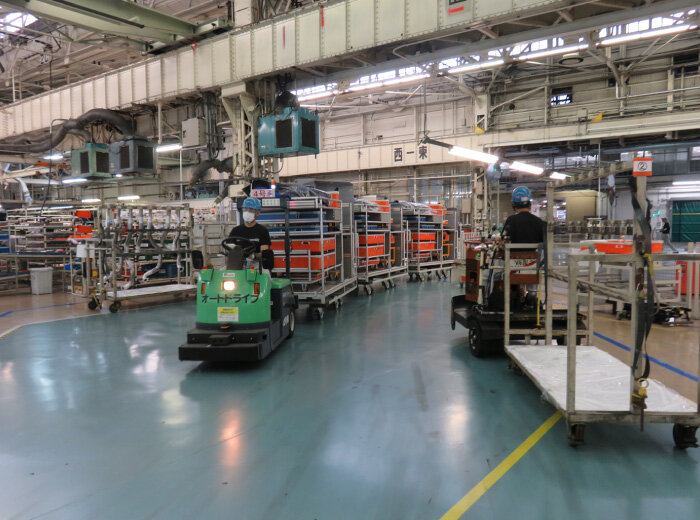

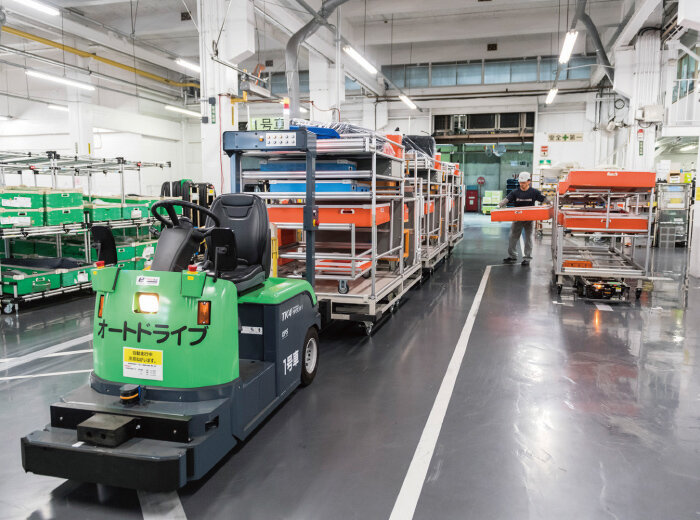
導入効果
- 手動だった台車運搬をキーカートに代替させることで、追加作業+αの時間削減を達成
- タグノバとキッティング作業者が無理なく作業をシンクロさせられるように
タグノバリモコン車でキットエリア内の自動搬送
世界初の量産電気小型トラック、eCanter(イーキャンター) ❷市場投入のニュースも記憶に新しい、三菱ふそうトラック・バス㈱。同社はアジア圏を担当するダイムラーAGグループの構成企業として、大型のスーパーグレート、中型のファイター、そして小型のキャンターと、トラックのフルラインナップ❸を揃えるほか、バス各種、自動車用エンジンで培ったノウハウを駆使した産業エンジンまで幅広く生産している。
同社の川崎工場❶は、そのトラック全ラインナップを生産し、世界170か国へ輸出しているほか、世界のマザー工場として、15か国以上のKD(ノックダウン)工場へコンポーネントを出荷しているメインファクトリーだ。
同工場では2016年、生産性と構内物流効率の向上を目指したフィッシュボーンコンセプト(図表1)に基づき、構内再配置(サイトストラテジー)の一環として全長約600mの組立ラインを完成させた。
小型、中・大型車の生産プロセスが、ラダーフレームのシャシー状態からパワートレーン、キャビンが搭載されて完成するまで、文字通り一直線に流れる究極の効率化フローに編成された。この製造現場のカイゼンを専門に受け持つプロフェッショナル集団が、OEM(Operations Efficiency Management・生産改善推進グループ)だ。同グループを統括するマネージャーの吉田圭一氏❹は語る。
「所内には他に、生産技術や協働型ロボットを専門に研究しているボットラボや、副作業長クラスを集めて自分の現場と異なるラインに短期で入り、集中的にカイゼンに取り組むSDW(Station Development Workshop)という部隊等もあるのですが、我々は現場に密接したカイゼンを重ねていくチームです。当社はFoF(Factory of the Future・未来工場)というイニシアチブのもと、インダストリー4.0に対応するべくオートメーションとロボティクスに投資し、工場内外のすべての物流を管理するITシステムを含め、効率化を進めてきました。そして今、さらにその先を行こうと〈e-shinka(イー進化・Jump to the Next Level)〉を合い言葉に、次のステージを狙ったカイゼンを進めている最中です」
ダイムラーグループのアジア戦略担う
こうしてOEMが進める最近のカイゼン活動の中から今回注目するのは、ライン間・ライン内の生産物流効率化のための、AGV導入プロジェクトである。OEMのアプローチには様々な手法があるが、いずれも費用対効果を重視すると共に、プラスワンの工夫を追求することが特徴。日頃から空きスペースを利用して、模型を用いたシミュレーションを繰り返すなど、常に創意工夫とレッスン&ランを絶やさない。
同グループの佐藤源一郎氏❺がある日、別部門の係長の持ち帰ったトヨタL&F高浜工場の見学資料を何気なく覗いた時に、安全道場、組立道場といった一風変わったフレーズが目に入ったので詳しく聞いてみると、「ここで紹介されている新しいAGVは、自分たちの現場フローを刷新してくれる、使えるツールかもしれない!」と直感で閃いた。それがキーカートとの出会いで、佐藤氏は即、トヨタL&Fの担当者にコンタクトを取ったのだという。
「私たちが工場内でやりたいことについて相談すると、競合機種よりも安価で、ニーズに応じた細かいカスタマイズもできる、との返事をいただいたので、それならまず1台導入してより多くの現場の人に見てもらい、感覚をわかってもらおう、と発注しました。それが2014年の夏のことです」(佐藤氏)。試しに1台注文されたキーカートが、今では同工場内で77台も稼働中だという。「費用対効果の点で群を抜いていることが証明されたから」とは佐藤氏の弁だが、では具体的に、現場でどのような急展開があったのだろうか?
同グループの松前利明氏❻に具体的な取り組みの経緯を聞いてみた。まず先入観を排除して、現場・現物・現実を調査・分析した結果、小型車両組立の艤装部品キット(インパネやシートなど部品の前段取り作業)エリアに、大きなカイゼンのポテンシャルがあることが分かった。
これがスタートになったと、松前氏は続ける。
「まず、人間がトーイングトラクタ(牽引車)を運転し、組立ラインに供給する部品が載った台車を運搬していた作業を自動化できないかと考えました。それがバッテリー式小型けん引車のタグノバリモコン仕様車の導入につながりました」
その現場を見てみると、組立ラインから3台の空台車を牽引してきたタグノバが停車し❼、ドライバーが運転席を下りた❽かと思うと、そこから先は無人状態で❾艤装部品キットエリアの方向へ進んでいった❿。
これはまさに“組立ラインへの供給は有人で効率的に高速移動し、部品キットエリア内では無人のリモコン走行が可能”という、タグノバリモコン車の機能を有効活用した好例といえそうだ。 ただし従来のオールマニュアル工程では、トーイングトラクタで牽引する3台の台車の積載時重量が2tを超えていた。これではタグノバのバッテリー負荷が大きくなってしまう。そこで1台700㎏あった従来の台車を設計し直し、アルミフレーム化することで400㎏にまで軽量化したという。まさにプラスワンの追求である。
未来を見据えたカイゼンの工夫がそればかりでないことを教えてくれたのは、治工具課TOS推進班作業長の木下繁樹氏⓫だ。
「内輪差がシビアに影響する狭い部品キットエリア内での正確な小回り性向上と、組立ラインエンドで切り離された3台の台車を再び牽引させる人力での作業⓬の負荷を軽減するために、従来4輪だった車輪を6輪化すると共に、車輪を変更し始動力を40%低減⓭するなど、マザー台車の製作プロセスにおいてトライ&エラーの繰り返しで無数の改良を施してきました」
まさにカイゼンのプロフェッショナル集団らしい突っ込んだアイデアが、随所に張り巡らされたのだ。このアルミフレーム台車は、全部で39台が工場内で稼働しているという。
ところで、タグノバ導入の際に、全工程を自動走行化する発想はなかったのだろうか?
すると松前氏は「確かに一度は構想しましたが、組立ラインには複数の部品供給箇所があって、牽引された積載部品が違う台車が同時並行的にライン内を行き来します⓮。一度にすべてを自動化しようとすると、走行する大量のAGVを一括制御するため複雑かつ大掛かりな仕組みが必要になる。そこで、組立ラインに届けるまでのプロセスは人の力を用いたほうがフレキシブルで効率的と判断したのです」と教えてくれた。
重いシートのリフトアップをキーカート+カラクリで自動化
どこまでを自動化し、どこまでを人間との協働にするのが真の全体最適か、その節度と判断こそが構内物流マネジメントの要諦なのだろう。続けて松前氏は、キーカートの事例について教えてくれた。
「キッティングエリアの中では、作業者が台車を人力で払い出し・引き取りしていたものをAGV化できないかと考え、こちらがキーカートの活用につながりました」
図表2はハイラインキット台車と左シートキット台車が隣接するエリアの一例だ。
まずハイラインキット側では、キットA工程でサブAssy(アセンブリ)作業が追加となり、作業量増加に伴う改善の必要が生まれたことから、従来手動だった台車運搬をキーカートに代替させることで、追加作業+αの時間削減を達成した。
一方、左シートキット台車側では、キットBで従来、10㎏以上ある重量物のシートをシート台車の高い位置に積載する人手作業の負荷が問題となっていた。そこでキーカートの駆動力を用いてスライド昇降させる、カラクリ機構を備えた新シート台車と組み合わせることで解決した(図表3)。
数々の創意工夫はまさにOEMグループの面目躍如といった印象だが、実際にこれらを導入・運用するには、苦心を重ねたようだ。治工具課TOS推進班カラクリ担当の朝倉孝雄氏⓯は話す。
「シート台車のカラクリ製作では、キーカートに牽引されたシート台車がスロープを登ることで、自動的に高い位置のキット台車へ作業者が投入しやすい位置まで上昇させる計画でした。しかし当初は床面の傾斜で台車が直進できなかった。そこで、この左シートキット台車も急遽6輪化することで直進性を確保しました。登坂時の負荷が高く持ち上がらない問題は、車輪の径を拡大すると共に、センター2輪を前後4輪よりややオフセットさせ、スロープでは進行方向側の4輪走行とすることでクリアしたのです」
聞けば聞くほど、カイゼンのプロたちの執念を感じる徹底ぶりである。現場でキーカートに牽引され、作業者の位置まで台車が持ち上がる仕組みを見てみると、そのスムーズさは見事の一言だった⓰~⓳ 。
サイクルタイムカウンターでキッティング作業(キーカート搬送)とタグノバを連携
さらにここにはもう1つ、効率化の試みが追加されていた。そもそも今回のカイゼンのコンセプトには、タクトタイムと連動したキッティングが対象として挙げられており、周回するタグノバの周期とキーカートの周期をシンクロさせる仕組みが求められていた。この課題については、タグノバ&キーカートと同時に導入されたサイクルタイムカウンター⓴により、次回のタグノバの到着時間を見える化することで、タグノバとキッティング作業者(キーカート搬送)が無理なく作業をシンクロさせられる環境が整えられたのである。
キットA工程で稼働するキーカートにも触れておかなくてはならない。こちらも単に2点間をピストン往復しているだけではないのだ。
この工程では重量の嵩む台車を、プラットフォームと平行する位置に、出発位置よりも若干オフセットさせて停めるという微妙な動きが要求されていた。これを正確に繰り返すには、台車の動線を往路と復路で僅かに変えて走らせる必要がある。そこで床に貼る誘導用磁気テープを中央付近で二手に分けることで、この制御を実現したのだ㉑~㉓ 。
「こうした実際の現場運用で直面する、細かいけれど重要な課題に対しては、作業パターンの設定がエクセルで簡単にカスタマイズできる、キーカートの“タスク30”の恩恵をヒシヒシと感じました。比較検討した他社製品にはない機能でしたから、本当に選んでよかったなと」
何よりもまず基本スペックの優位性とコストパフォーマンスの裏づけが必要なのは当然だが、加えてフレキシブルな現場対応力を備えていたことが、トヨタL&Fのソリューションの「選ばれる理由」となっていた。短期間に一拠点の様々な部署で、トータル70台超の導入を達成した原動力がここにある。
もちろん川崎工場OEMチームのカイゼンが、これで完結したわけではない。「例えばもし、タグノバが屋外でも使えるようになれば、新しい可能性が生み出せるのでは……」と語る松前氏の未来構想図には、次の一手が既に描かれているのかも知れない。
本事例における導入商品
CASE STUDY
その他の導入事例
-
トヨタモビリティパーツ株式会社 茨城支社 様
t-Sort 3Dの導入で、作業者負担や仕分けミスを削減し、高効率な仕分けを実現。
導入場所:倉庫・物流センター
業種:小売・通販・卸売 / 自動車・輸送機器
導入商品:仕分け機・ソーター -
トヨタモビリティパーツ株式会社 様
バケット用自動倉庫の導入で、作業者の労働環境改善を実現。
導入場所:倉庫・物流センター
業種:小売・通販・卸売 / 自動車・輸送機器
導入商品:自動倉庫 -
神谷鉄工株式会社 様
移動ラックとKEY SO-COのセット導入で、保管、作業効率の向上と作業の標準化を実現。
導入場所:工場
業種:自動車・輸送機器
導入商品:移動ラック(移動棚) / 情報システム -
三和パッキング工業株式会社 様
材料・完成品の入出庫や工場棟と倉庫棟間の搬送作業を自動化し、省人化を実現。
導入場所:工場
業種:自動車・輸送機器
導入商品:自動倉庫 / AGF(無人フォークリフト)