7万点の保守部品の即納体制を確立した、魅せられるパーツセンターで拡販活動を支援。
株式会社アマダ 様
https://www.amada.co.jp/
業種:鋼鉄・金属
導入商品:自動倉庫 / 移動ラック(移動棚) / 情報システム

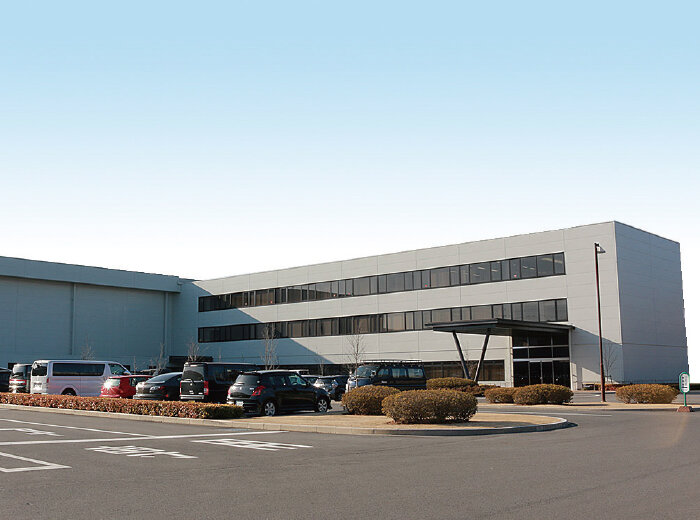
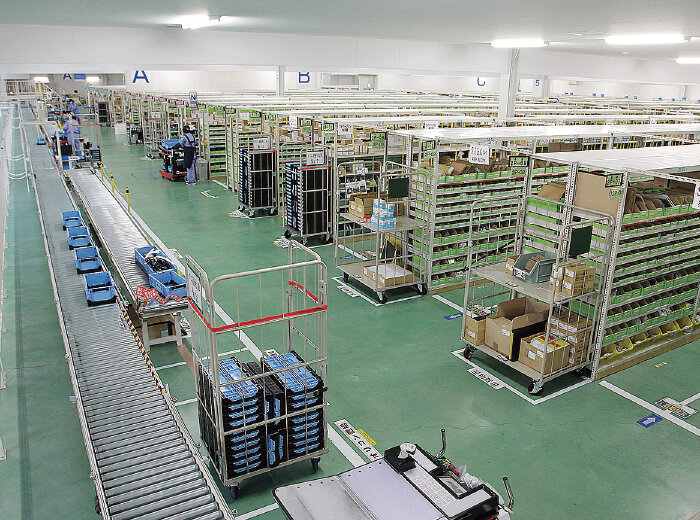
導入効果
- エンジニアリングから運営までのすべてをワンストップで支援
- 高出荷頻度品はラック、低出荷頻度品は空間を活かした自動倉庫を活用
金属加工機械の総合メーカー、アマダ様。ファイバーレーザーマシンの開発・製造に力を注いでいます。そうした新製品の開発に加え、取引のあるお客様に保守用パーツを迅速にお届けするのも重要な使命の1つです。その役割を担うパーツセンターを2009年に移転・新設した際にアマダ様が望まれたのは、パーツセンターを運営する理想的なしくみの導入です。
依頼を受けたトヨタL&Fは、エンジニアリングから導入する機器の選定・設計、運営、運用改善支援までをワンストップで担当。旧センターの課題であった作業員の経験に頼っていたピッキング作業や、増え続ける在庫の管理方法の改善などを含めて、全体最適のソリューションを行いました。完成した新パーツセンターでは、稼動後も運用改善を積み重ねることにより、作業効率や出荷精度などのさらなる向上を実現しています。
❶入荷エリア
入荷したパーツは荷姿別・保管エリア別の仕分を行います。重量物や長尺物は大物保管エリアへ。小物や品質管理品はエレベーターで3階に搬送。
❷大物保管エリア
重量物や長尺物は、大物保管エリアに設置された移動ラックに保管。
❸ケース保管エリア
ケース自動倉庫を導入し、増え続ける多種多様な保守パーツの保管に対応。
❹入荷梱包作業エリア
3階に搬送した小物パーツは入庫前に梱包。これにより出荷時の梱包作業の手間を軽減することが可能。
❺入荷搬送コンベヤ
梱包した小物パーツはコンベヤで入庫先に搬送。
❻小物保管エリア
中・高出荷頻度の小物パーツは、中軽量ラックにフリーロケーションで保管。
❼マルチピッキングカート
アマダ様と共同開発したRFIDピッキングカートを使用。最大4オーダー分のピッキングを同時に行うことができ、入出荷兼用で使用することが可能。
❽ポカヨケ機能
モニターに数量やロケーションなどのピッキング指示が表示。また、初心者でもミスのない正確なピッキング作業ができるよう、LEDによる作業間口指示や音声ガイドを導入。
❾小物ピッキングエリア
収容箱などを活用し、荷姿に合わせた高密度保管を行うとともに、ピッキング動線の短縮と誤出荷防止に貢献。
❿出荷搬送コンベヤ
出荷品を出荷梱包エリアへ搬送。
⓫出荷梱包エリア
出荷検品を行い、国内・海外などの出荷先別に梱包。海外梱包については、ネット重量を計測する他、木枠梱包にも対応。
本事例における導入商品
CASE STUDY
その他の導入事例
-
株式会社ヤマヒロ 様
バケット用自動倉庫ラックソーターBの導入で、小口出荷対応、および作業の平準化・標準化を実現。
導入場所:工場
業種:鋼鉄・金属
導入商品:自動倉庫 -
日本精工株式会社 様
移動ラック+AGF(自動運転フォークリフト)の導入で、保管効率の向上と入出庫作業の自動化を実現。
導入場所:工場
業種:鋼鉄・金属
導入商品:移動ラック(移動棚) / AGF(無人フォークリフト) / AGV・AMR -
三進金属工業株式会社 様
約120回/日の製品搬送・入出庫作業を自動化。自動運転フォークリフト(AGF)の導入により人員の最適配置が可能になり、稼働率向上を実現。
導入場所:工場
業種:鋼鉄・金属
導入商品:AGF(無人フォークリフト) -
株式会社エノモト 様
在庫のロケーション管理を実現し、作業効率や作業品質が大幅に向上。
導入場所:工場
業種:鋼鉄・金属
導入商品:情報システム