約120回/日の製品搬送・入出庫作業を自動化。自動運転フォークリフト(AGF)の導入により人員の最適配置が可能になり、稼働率向上を実現。
三進金属工業株式会社 様
https://www.sanshinkinzoku.co.jp/
業種:鋼鉄・金属
導入商品:AGF(無人フォークリフト)
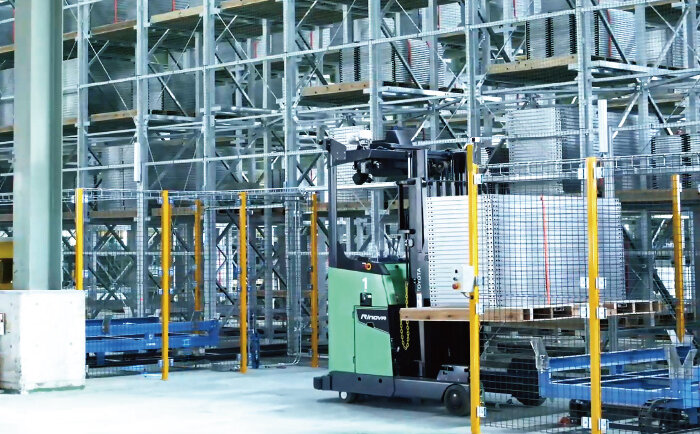
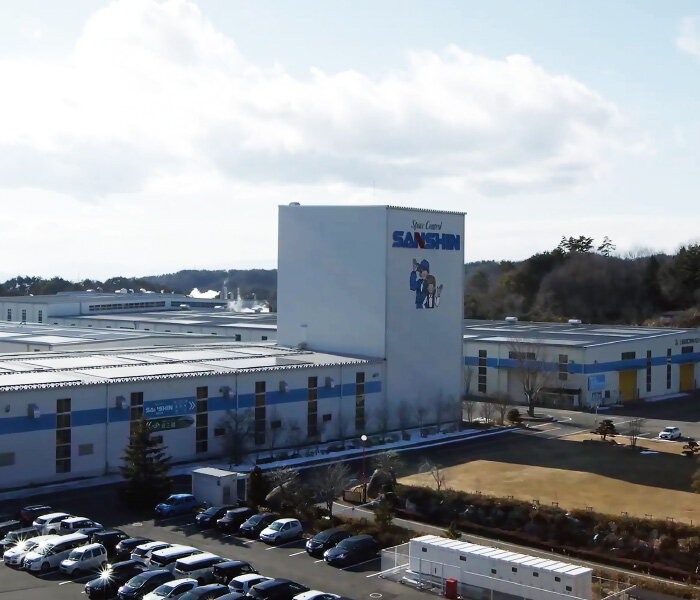
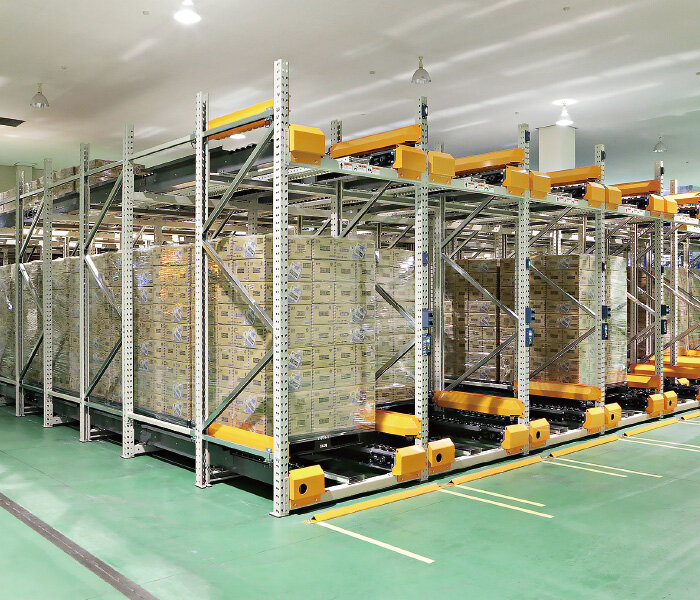
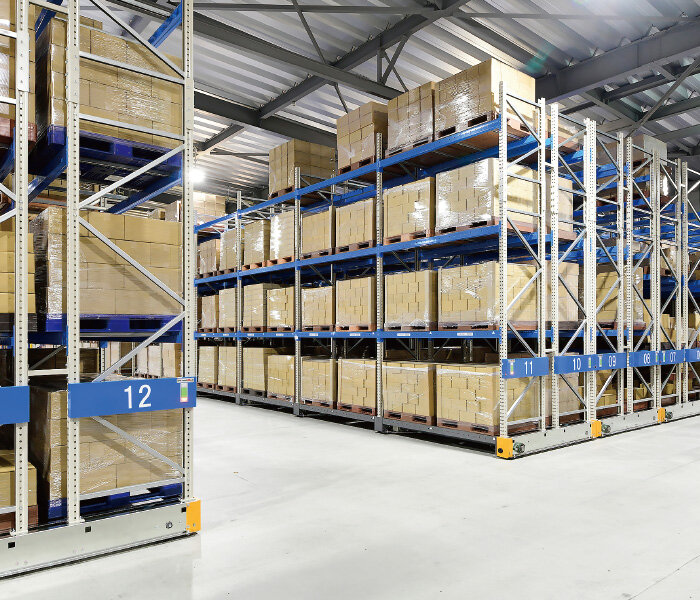
導入効果
- 自動運転フォークリフトの導入により、省人化(棚板ライン人員5名→4名)と工場全体の稼働率向上(約4%)を実現
- 各種センサーをはじめ、ブルーライト、大音量メロディーホンなどの数々の装備を自動運転フォークリフトに設定し、安全な作業に貢献
製品の搬送作業が従業員の大きな負担に
三進金属工業様は、空間を効率的に有効活用する物流保管設備機器をはじめ、実験・研究設備、植物工場、鋼構造物など生産性の高い空間づくりを通じて社会に貢献しています。
福島県平田村にある同社の福島工場は、アジア最大級のラック生産力を誇るだけでなく、自然環境保護や地域活性化の取り組みを実践しています。そんな福島工場の中核を担っているのが、2万7,000㎡の広さと充実の設備を備えた福島第1工場です。従来の課題について代表取締役専務の新井様は、「棚板の成型ラインが4本あり、50枚出来上がるごとに作業者がハンドパレットで払い出すという状況でした。多いときは約6,000枚/日の棚板を生産し、次工程の塗装ラインへの入庫などの搬送作業が約120回/日にもおよび、作業者に大きな負担が掛かっていました」と話します。
そこで、搬送・入出庫作業の自動化を検討し、トヨタL&Fの自動運転フォークリフトAGFを導入しました。「AGF実機を初めて見学させていたただいたのは、トヨタL&Fカスタマーズセンター大阪です。そしてさらに福島第1工場でも実際に入出庫作業を自動で行うAGFのデモを目の当たりにしたときは、本当に夢を見ているようでした。『この商品は間違いない』と感じた瞬間です」と新井様。
AGFの導入で、省人化・稼働率向上を実現
導入したAGFは、レーザーリフレクタ方式を採用しており、作業エリアに設置された反射板の位置をレーザースキャナで検出し、車両の自己位置を高精度に検知するシステムを搭載しています。AGFの使用状況は、完成した棚板の生産ラインからの荷取り・自動倉庫への搬送・入庫作業と自動倉庫から再出庫した棚板の塗装ラインへの搬送作業を合わせて約16時間/日です。
「AGFを導入したことにより、棚板ラインの人員を5名から4名に1名の省人化を図ることができました。その結果、工程負荷の大きいラインやその他の工程に人員を充てることが可能になり、工場全体の稼働率や生産性も向上しました」と新井様。また、福島第1工場は作業者や有人フォークリフトの往来も多い現場ですが、各種センサー、ブルーライト、大音量メロディーホンなどの装備をAGFに設定することにより、安全な作業に貢献しています。
福島工場では、他にも多くの人手を必要とする工程があることを踏まえ、「今後、AGFの横展開による更なる搬送改善を進めていきたいです。さらに自社商品のライブストレージや自動倉庫の追加導入と併せて在庫管理やピッキング工数の削減の他、リアルタイムの進捗管理が行える工場内物流の“見える化”も目指します」と新井様は展望を語られました。
自動運転フォークリフトAGFで製品の搬送・入出庫作業を自動化し、工場全体の稼働率向上を実現
■AGF運行図
❶空パレットの搬送
完成した棚板を積み込むための空パレットをピックし、棚板生産ラインへ自動搬送。
❷棚板ラインから荷取り
4本の生産ラインから完成した棚板を順次荷取り。
❸自動倉庫へ搬送・入庫
4本の生産ラインから荷取りした棚板を自動倉庫へ搬送・一時入庫。
❹自動倉庫から出庫
次工程の塗装ラインの準備が整うと、自動倉庫から再出庫された棚板を荷取り。
❺塗装ラインに搬送
自動倉庫から荷取りした棚板を次工程の塗装ラインへ自動搬送。
レーザーリフレクタ方式
作業エリアに設置された反射板(リフレクタ)の位置をレーザースキャナで検出することにより、機台が高精度に自己位置を検知するシステム。床面工事が不要のため、賃貸倉庫など床面工事ができない現場でも導入が可能。
安全装置
各種センサー、ブルーライト、大音量メロディホンをAGFに設定することで、安全性を確保。